Summary
This 8 week internship—my first job—has been one of the hardest, yet rewarding experiences I've had.
I've enjoyed and learned a ridiculous amount from designing parts for and operating the DMLM (Direct Metal Laser Melting) 3D printers, performing solder fatigue analysis for commercial satellites, creating a deployment mechanism for a next-gen solar array that relies on 3D printed parts, and more...
How I got the Internship
After my 2020 summer internship @ NASA fell through due to the start of the pandemic, I was determined to get an internship this summer. Applying for a summer internship as a high school student is exceedingly difficult, most big tech companies don't take high school students and many startups weren't hiring due to the pandemic. After cold emailing a dozen companies hoping for a response, I looked for other companies that may be accepting high school applicants in the midst of the pandemic.
I contacted one of my good friends who interned at Lockheed Martin Space the previous summer, and I asked him if get me in contact with the recruiter. After a month of waiting and another month of back and forth, I was finally asked to send in my resume. The recruiter was impressed and invited me to an interview. I prepared for a solid 2-3 hours for the interview and after the interview, I felt as if I killed it.
I got a call the next day with confirmation that I got the internship! I was beyond elated and accepted the offer that I got within the end of the week. I later got on a call with my managers and the recruiter, my manager told me what I will be doing during the internship and preparation for my first day.
My Expectations going into the Internship
Going into the internship, I presumed I would be be mostly doing menial work and shadowing my coworkers. This would include creating presentations, filling out forms based on a template, etc. I was expecting to be assigned tasks and interacted with as a high schooler, rather than a college graduate.
I highlighted a few of the goals that I had going into my internship in my resume. I was hoping that I would be able to fulfill at least 2-3 of these roles to a limited capacity:
- Industrial Additive Manufacturing
- 3D modeling and fabrication
- Engineering Technician
- Proof of Concept design prototyping
- Contribute to research in aerospace
- Research in emerging technologies
- Gaining work experience in the industry
- Experiencing Start-up culture. (n/a for Lockheed)
My Internship Experience
The First Day: Even from on first day, my expectations were blown out of the water. The first indication of this was my badge. My badge didn't say "High School Intern" or even "Intern", it said "Employee".
My manager showed me to my cube, which was huge! I was expecting to have a small desk that was recently vacated, but instead, I got a full on cubical– comparable to full-time employees–along with a proper engineering laptop and dual monitors. Not long after I settled in, I got my first assignment from my managers, I was to learn the basics of solder fatigue analysis with a co-worker and submit it by the end of the month. Rather than checking over someone's work, I was doing tasks given to entry-level, full-time employee!
Throughout the remainder of my internship, I wasn't given a SINGLE menial task, this means a lot to me. Every task that I was assigned challenged me in one of two ways: Either I would have to learn a whole new set of concepts, such as learning electronic components and their properties relating to solder joints, or I would be given a complex task and very little direct guidance–simply a list of criteria and constraints!
Additive Design Manufacturing Center
Working in the ADMC was a dream come true for me; over the past 7+ years, I have been obsessed with Plastic/Resin 3D printers and have ended up incorporating the manufacturing process into many of my projects–as you could easily tell from the rest of my blog; science fair, robotics, and even solutions to simple problems. Getting to work with metal 3D printers that are capable of 99.95%+ solid titanium, aluminum, copper, etc. was the highlight of my summer.
When I was first looking into internships, I remember reading about this article. This is the spark that made me want to intern @ Lockheed Martin Space over anywhere else.
After reaching out to one of the lead engineers at the ADMC, I was given a tour of the absolutely incredible facility. I immediately told him at the end of the tour that if there was any work that I could do here, I would love to do it. To my delight, he told me he would like me to work on some tasks starting the next day!
The least glorious and most tedious part of the whole metal 3D printing process is to recapture unused metal powder from the build plate (this is exponentially harder for larger printers, like the X Line 2000R I worked on). This is done through a cramped glove box that is made inert with Argon gas (to prevent spontaneous combustion of the powder) using a hose attached to a vacuum.
I set out to create a easy tool change system that would allow the operator to more quickly and more thoroughly remove metal powder from the crevices of the part. This not only saves hours of manual labor, but also cost since trapped metal powder that is removed in the vibration machine is oxidized, making it unusable. I fully dedicated myself to this task and was able to create the hose tool changing system in 2 days. After I got that working, I printed it out of plastic and tested it. It worked so well that the lead engineer decided to take it to other locations the following week!
Since the default configuration for the hose is attached to a lance (a large metal tube), I continued by creating a docking station that allows the operator to easily swap between the lance, and a custom tool–one that can easily be changed with the tool changing system.
The hardest part of the design process was designing a product that was all of the following at once; printable in plastic, printable in metal, air-tight, and quick to access. I spent 2 weeks and dozens of iterations getting the design tuned and finalized. I got to see a plastic prototype functioning in the machine, however due to a running print job, I wouldn't be able to see the final metal result.
In addition to designing the tool changing system, I was interested in the materials that were used to create isotropic 3D prints. I was shown to the "Universal Testing Machine", this machine was able to effectively pull on the material, in this case tensile bars that were printed scattered around the part. After measuring the cross-sectional area of each bar and loading it up into the machine, I would run the test.
After 10 minutes or so, the bar would snap extremely loudly and a stress/strain graph would be available. Using the material properties, elastic/plastic deformation, cross-sectional area, and other derived values, we would be able to certify whether the manufactured parts were within specifications.
In the process of doing this, I learned a lot about the different material properties themselves and different testing methodologies. After having some scholarly discussions about the material properties of different metals and how different fabrication/post-processing affect them, I suddenly realized how interesting materials science is. As I am writing this, I am pondering my path forward and contemplating whether I want to pursue material sciences further.
Working @ the ADMC was definitely the highlight of my time @ Lockheed. Looking back, I still find it incredible that my curiosity about 3D printing from Maker Faire in 5th grade has driven me so far!
Solder Fatigue Analyst
My first major assignment was that of a Solder Fatigue Analyst for the Electronics Packaging team. By the end of my internship, I had completed analysis on several boards for different satellites!
There are a huge variety of components that Lockheed Martin uses and for many of the components, different packages are available (such as leaded and leadless). For each of these packages, the parameters and equations to use widely differs; I taught myself from documentation which formulas to use for accurate results.
After I got a package list from the list of components on the board–a process of its own, I performed the solder fatigue analysis using Excel and corresponding formulas for the package. For packages that would fail prematurely into their life, I wrote recommendations into a Powerpoint that outlines when it would fail and some alternative packages. If the package needs to be modified as well, I indicated the modifications needed for the package to pass. I presented the powerpoint, which contained the results from my analysis and any recommendations, to the PCB Engineers and answered their questions. Besides the initial board, this entire process was completed by myself.
The biggest takeaway for me was not the skills or lessons I learned, rather it was the systems-level understanding I developed regarding the design requirements and validation standards for any space-bound body due to the relentless hostility of space. I participated in various tours–thermal vacuum (TVC) testing, to name one–and many of the questions that I had about projects that I was supporting (or learning about) were about the reasons for design decisions. Solder fatigue analysis is one such area, most boards simply don't experience the frequent, extreme temperature gradients that satellite boards do.
Deployment Mechanism for 3D Printed Solar Array Truss
Due to the cyclical nature of my workload, I asked my manager for another project, preferably one that included elements of CAD, rapid prototyping, and moving assemblies. The next day, I was brainstorming a complex deployment mechanism with a fellow post-graduate intern that sits behind me.
Without going too far into the specifics of the project, there is a Solar Array that is suspended from the ceiling on a linear rail track. While the solar array is able to deploy on its own due to the existing innovative "spring" design, the linear rails at the top are over 50 years old and prevent the truss from deploying.
As part of the demo that we needed to perform for our customer, we wouldn't be able to assist the deployment of the structure in any way. The biggest problem was gravity, we needed to simulate a zero-gravity deployment in a regular clean room.
The solution that my coworker and I came up with was a multi-pulley system that assists the deployment of the truss without human intervention (as there wouldn't be any in space).
We spent the next 2 weeks iteratively designing our vision in Creo Parametric 4. I originally hated this CAD software, to even create simple structures (like threads) or patterns, would take a bunch of supporting features. Even after learning the software well, I still hate it; however, I've grown to appreciate certain aspects of it– such as its implementation of the middle click.
After each part was designed, we would upload the print over to the innovation garage's–the local makerspace with 3D printers, routers, tools, etc.–3 working Prusa i3s. One of us would run down and start the print and watch the first layer go down and tune the printer if needed. Our workflow was pretty much: design–review–print–test–revise. After 5 revisions, we had a working prototype and made our final deliverable 4 weeks early!
Besides the knowledge that I gained as part of the assignment, I furthered my ability to self-learn, to concisely and precisely ask questions, and to communicate complex, abstract ideas with my coworkers.
My Takeaways
As mentioned earlier, I was under the expectation of meeting a few of my goals for the internship to a limited capacity, however, by the end of the internship, I had met practically all of them!
- Industrial Additive Manufacturing - ADMC
- 3D modeling and fabrication - ADMC/Solar Array
- Engineering Technician - ADMC/Solar Array
- Proof of Concept design prototyping - Solar Array
- Contribute to research in aerospace - ADMC/Solar Array
- Research in emerging technologies - ADMC/Solar Array/Solder Fatigue
- Gaining work experience in the industry - ADMC/Solar Array/Solder Fatigue
Looking back, the time that I spent working was 100% worth it. I not only gained valuable work experience in the areas that I am passionate about, but also connected with amazing people that appreciate my curiosity and are more than willing to dedicate their time to help me learn.
Working with professionals, I got to experience first-hand the true dedication and professionalism that is apparent in the workplace; Including how to effectively communicate professionally with my coworkers–I was unsure at first and ended up calling a manager as I would call a teacher.
I also have greater clarity in my career direction/major. I was initially focused on being a young entrepreneur and minimizing my time in industry. Additionally, I wasn't as interested in doing research and thought to favor more tangible work, such as design or fabrication. Due to the internship, my opinions and inclinations have definitely shifted. I learned about technology readiness level (TRL) during a chat with my coworker from the ADMC (we were visiting the Palo Alto Campus), TRLs are used in industry to decide whether technologies are ready for missions, but I found that this metric fit really well into my interests.
Being an entrepreneur would be the equivalent of bringing an idea from TRL 1 all the way to TRL 8 or 9 as fast as possible. While I am still interested in doing that, I'd now like to gain more experience in the lower TRL levels. Much of the work that I have been doing has been in the higher TRLs–designing, fabricating, and machining parts. I've already had experience in the 6-9 range, however, my direct experience in the 1-5 range is limited. This is where I think I will be able to grow the most.
Photos
As a parting gift from my co-workers, I got a really cool 3D printed desk item that is made of solid metal!
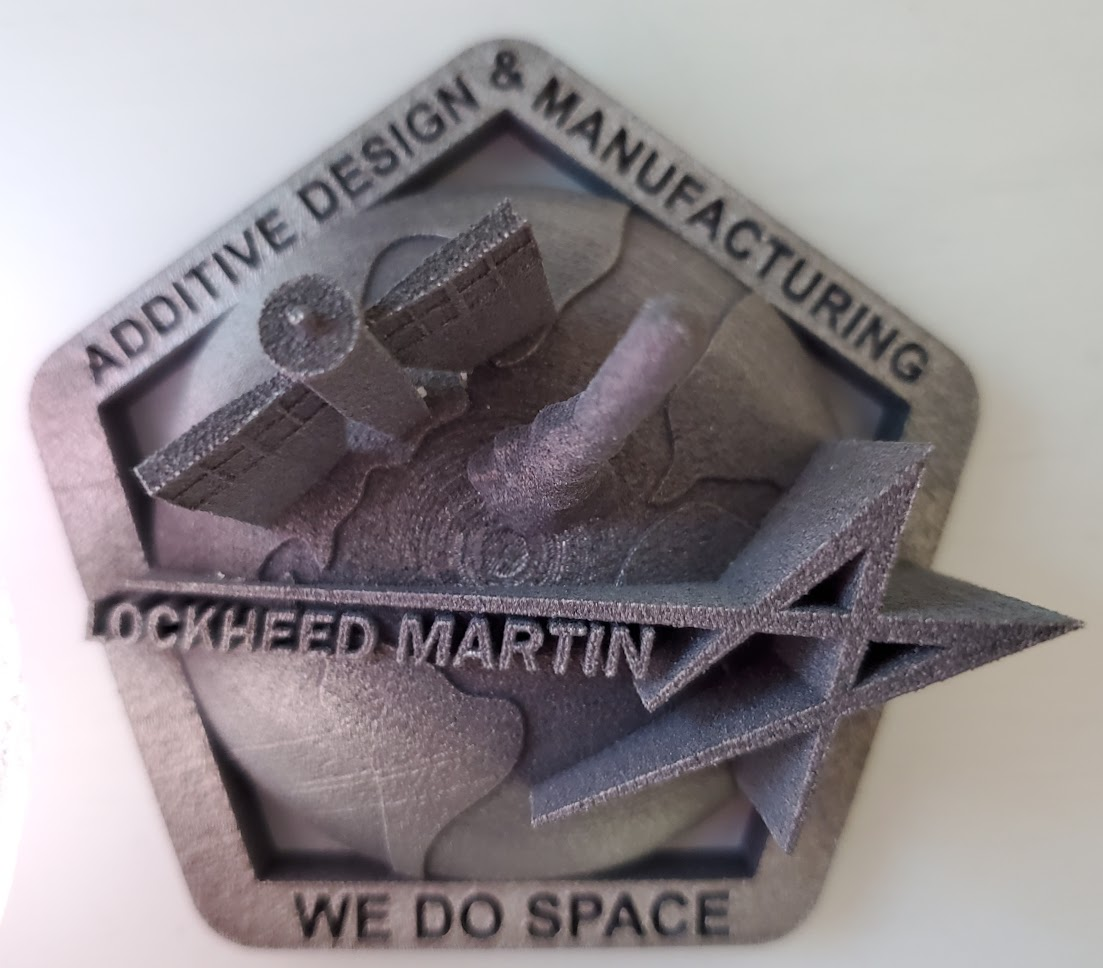
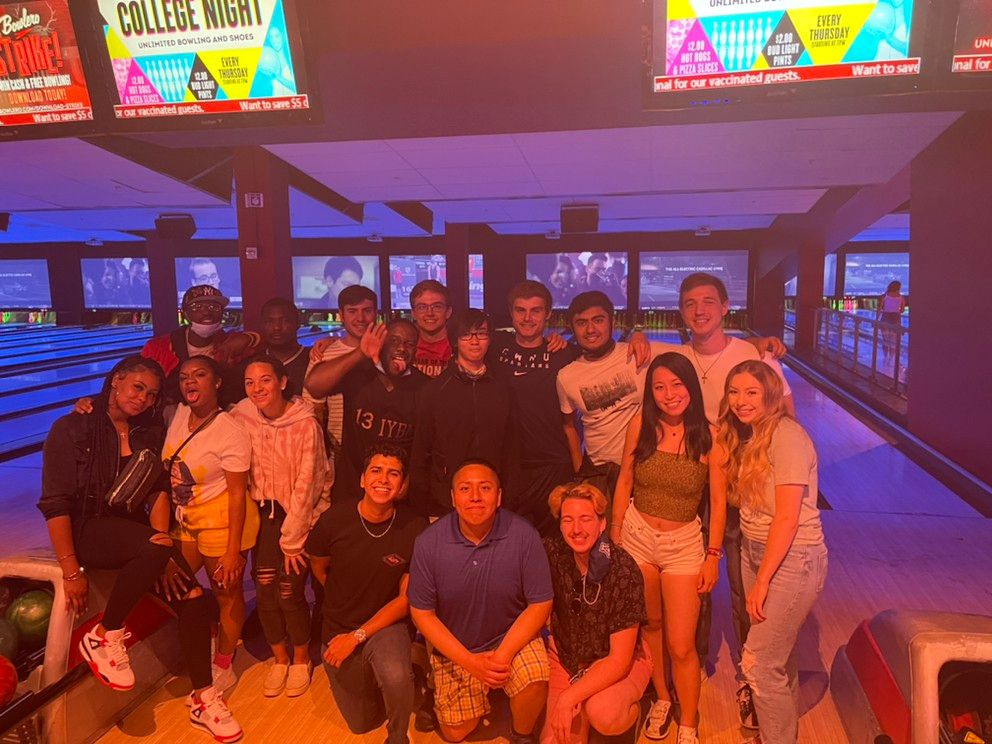
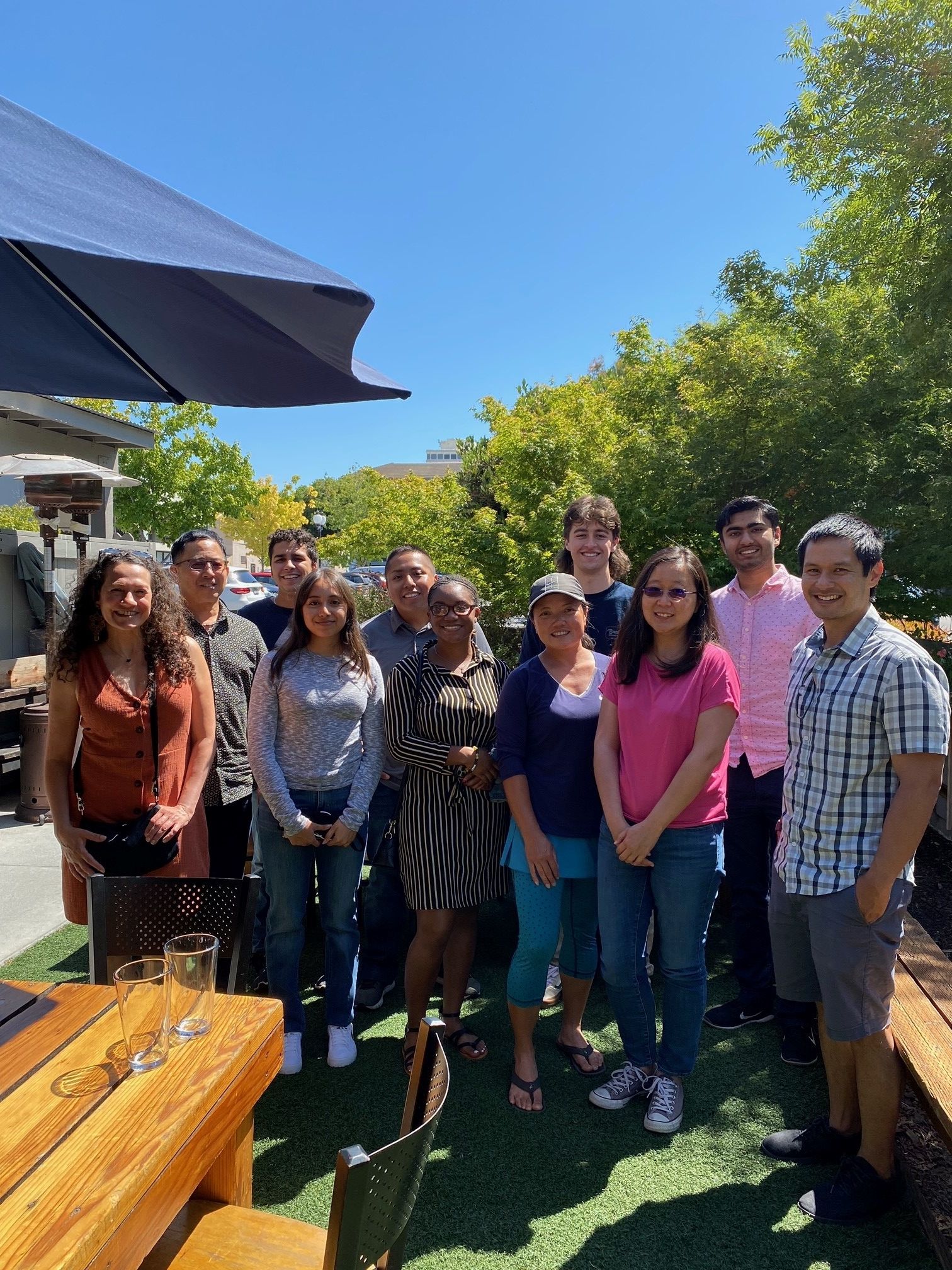
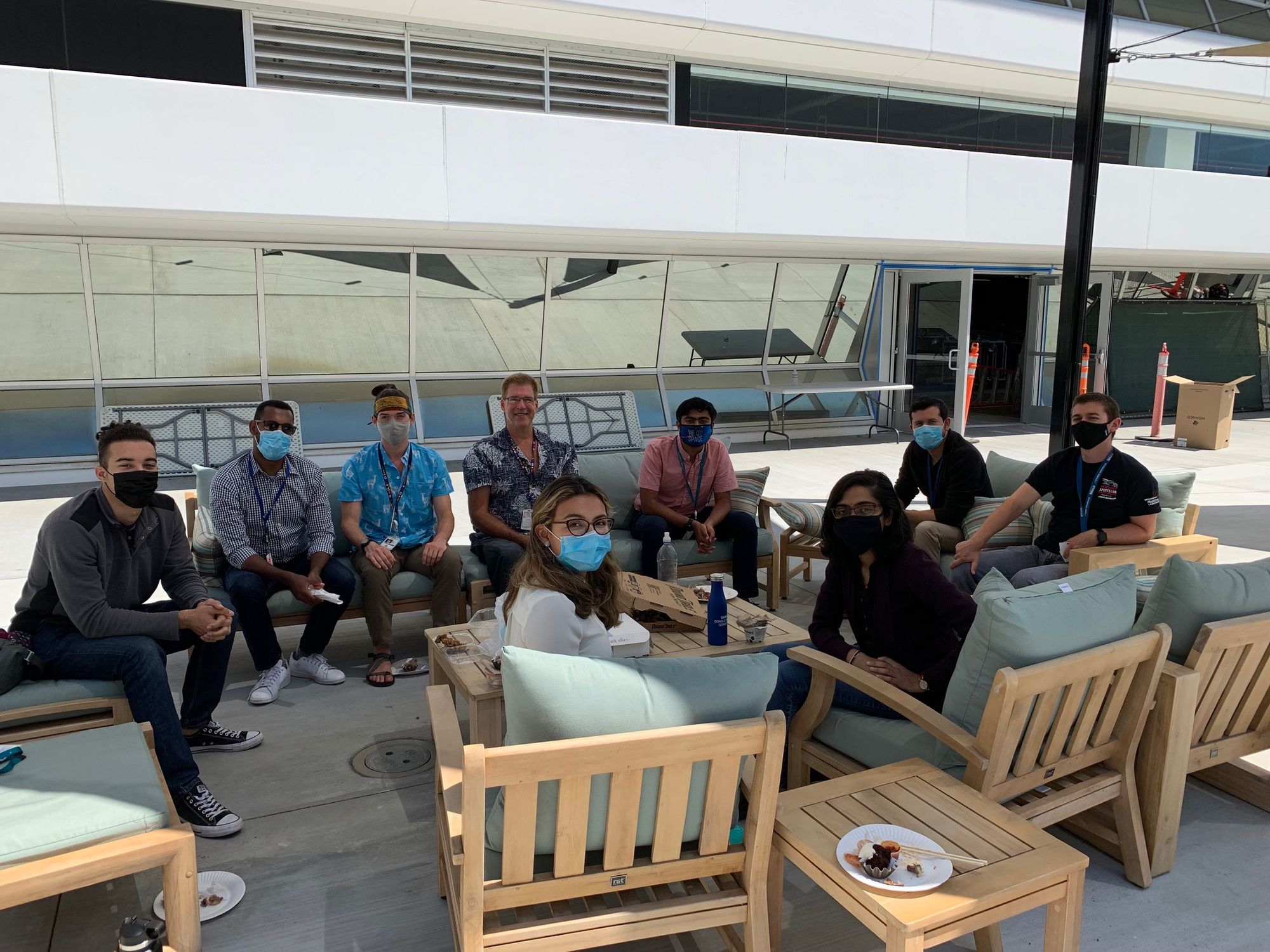
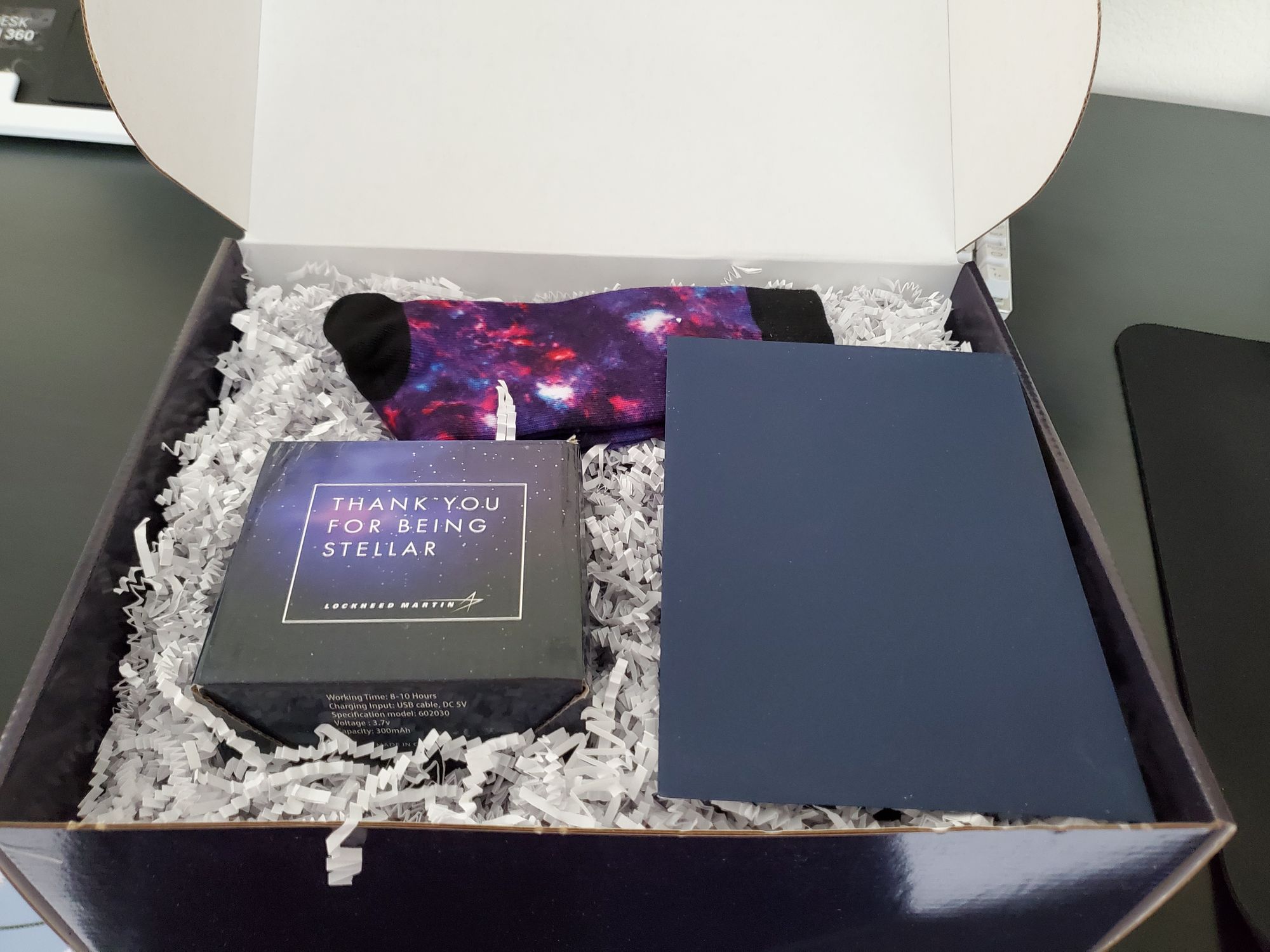
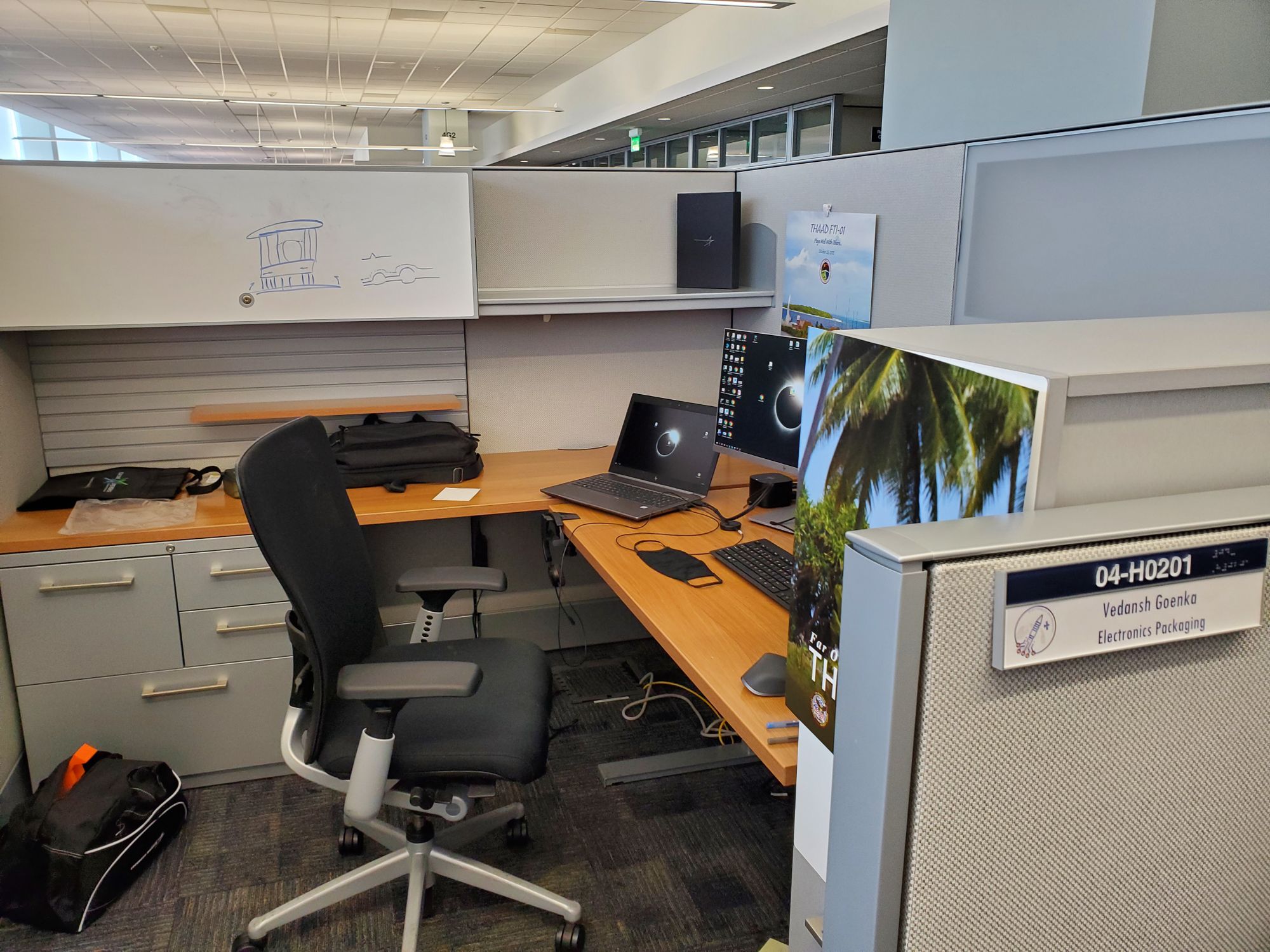